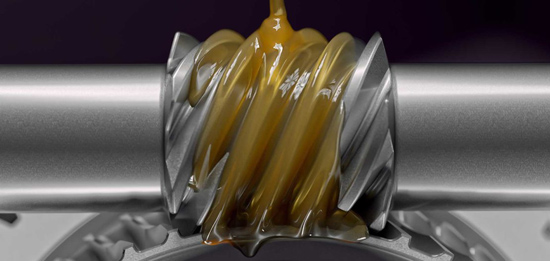
Friction is unavoidable in mechanical systems, but the right kind of lubrication will minimize its extent and impact. In many cases, lubrication is provided to mechanical systems via grease, oil, or air-oil systems. These lubrication systems help reduce energy losses at the interface, prevent heat buildup, minimize wear, and prevent corrosion.
Although grease, oil, and air-oil systems each offer the same general benefits, the choice of which one to use will vary based on your unique application.
Grease Systems
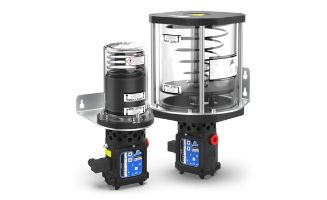
Grease is a thick, viscous fluid made by adding a thickener to lubricating oil. This prevents it from flowing readily but ensures it remains where it was deposited.
In the most straightforward systems, grease is pumped in via a grease fitting using a hand-actuated pump. A greased joint usually has an exit port for old grease to leave as fresh grease is pumped in.
Modern equipment often incorporates grease systems that automatically dispense grease to multiple fittings. These reduce consumption and prevent over-lubrication while ensuring each joint or surface receives the lubrication it needs. Another advantage is that they reduce the maintenance department workload by automating the greasing process.
Advantages
- Remains in place when equipment isn’t running.
- Protects against ingress of contaminants.
- Won’t drip out onto floors.
- Works in environments that are too challenging (due to heat, pressure, or moisture) for oils.
- Available in grades suitable for use with food and beverage processing equipment.
Disadvantages
- Can’t be recovered, filtered, and reused.
- Can harden over time and lose its lubricating properties.
- Doesn’t carry heat away from the joint.
- May result in higher friction than oil lubrication systems.
- More complex than oil-based systems.
Best Use Cases
- Wherever it’s impractical to run feeding lines for oil (suspension joints, for example).
- Rolling element and plain bearings.
- Industrial equipment where there are locations suitable for grease fittings.
- Rail cars and railroad track equipment.
- Mobile equipment used in agriculture and construction.
Oil Systems
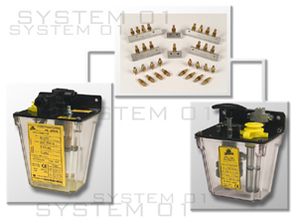
Oil is a low-viscosity fluid that flows readily, adheres to surfaces, and resists moderate pressures, all of which make it an excellent lubricant. Oil lubrication systems are divided into two types: total loss and recirculating.
In a total loss oil lubrication system, oil is delivered at a measured rate to where it’s needed through feeder lines or galleries machined or cast into the equipment. Delivery is usually by pump, although gravity systems have been used in the past. Once dispensed, the oil is not recovered.
Most modern machinery uses recirculating oil lubrication systems. These hold a supply of oil in a tank or sump, pumping it to where it’s needed through feeder lines or galleries. The system may be designed to drain the oil back into the tank under gravity or have return lines built in. The system will include one or more filters to remove fine particles and contaminants that would otherwise accumulate.
An oil lubrication system may also incorporate a cooler to lower the oil’s temperature before it is reused.
Advantages
- Contaminants are carried away from the joint or interface and filtered out.
- Oil flow removes heat.
- Less friction and parasitic energy consumption than with grease systems.
- Delivery system runs without needing human input.
- Can be formulated for an extensive range of temperatures and pressures.
- Specialized grades of oil are available for use with food and beverage processing equipment.
Disadvantages
- Oil can drain away from the joint when the pump isn’t running.
- Filtration system requires periodic servicing.
- Difficult to ensure vertical surfaces receive an adequate flow of oil.
- Requires high-quality seals and gaskets to prevent leaks.
- Doesn’t keep out contamination the way grease can.
Best Use Cases
- Industrial machinery, particularly where shafts turn at high speeds, as in CNC machine tools.
- Transmissions and gearboxes, where heat removal is a priority.
- Mechanisms where access is difficult (such as transmissions and gearboxes).
- Engines and turbines.
- Air compressors.
Air-Oil Systems
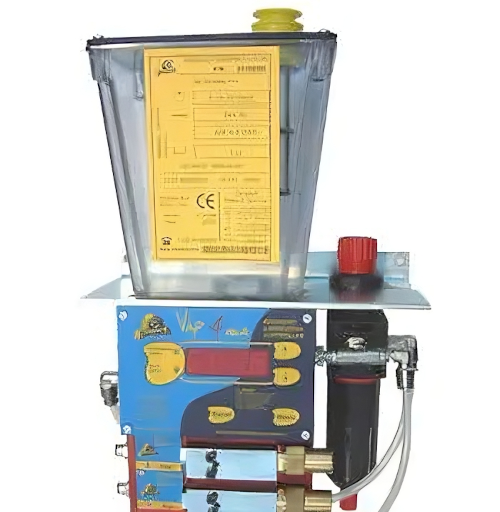
Air-oil systems apply a thin film of lubricant to surfaces or interfaces and use compressed air to carry fine droplets of oil to where lubrication is needed.
The heart of an air-oil lubrication system is the mixing valve, where oil is entrained in the moving air. This often includes a metering capability to ensure oil is delivered at a precise rate. Other system components include a pump, an air control valve, and a filter. In some applications, an oil streak sensor might also be included to verify that oil is being delivered as required.
Oil is often recovered after use in a separator, so it can be cycled through the system rather than lost.
Air-oil lubrication systems provide “minimum quantity lubrication,” often with a low-viscosity oil. They are also used in machining and forming applications, aiding cutting and material deformation.
Advantages
- Minimizes oil consumption.
- The air stream creates positive pressure around the joint, helping to exclude contaminants.
- Avoids oil carryover to other surfaces.
- Cooling is provided through the air stream rather than the oil.
- Minimizes frictional losses.
- Environmentally friendly.
Disadvantages
- System is more complex than standard oil or grease systems.
- Needs a dependable supply of clean, dry, compressed air.
- Requires regular preventive maintenance to avoid clogged nozzles and filters.
Best Use Cases
- Bearings in high-speed spindles, as used in CNC machine tools and turbines.
- Chain lubrication.
- Machining and forming processes.
Find Your Solution
Effective lubrication is key to ensuring equipment longevity and consistent performance, improving product quality, and reducing operational costs. Whether you’re designing equipment that requires a lubrication system, developing a metal cutting or forming process, or purchasing industrial machinery, DropsA is here to help you find the best solution.
Contact us today to speak with one of our experts, or take a look at our blog for more resources.